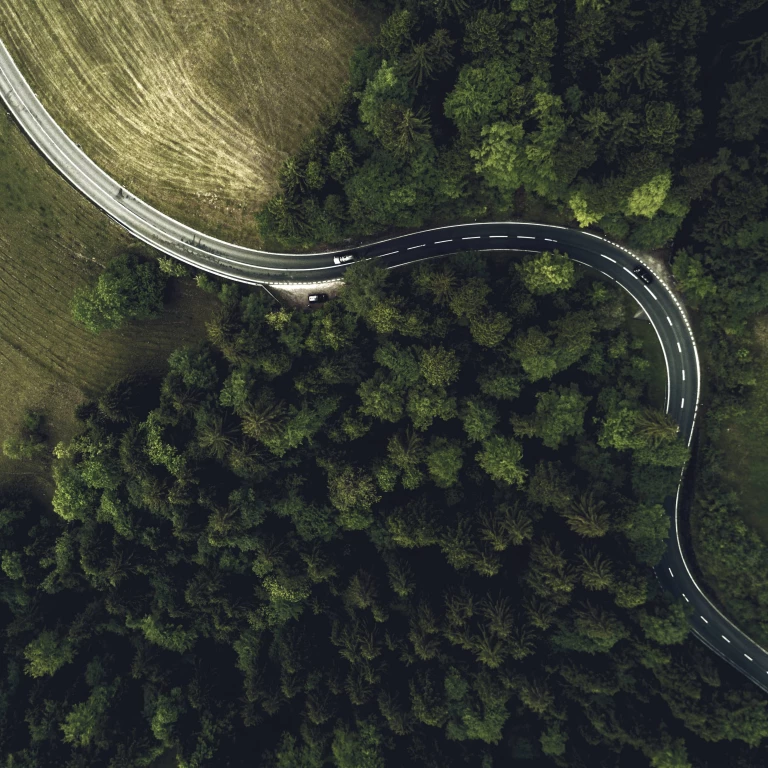
Our Impact and Commitments
Guided by the belief that we grow ourselves by helping others, BCG prioritizes collaboration, challenging the status quo, and continually striving to create socially transformative businesses that align profit with purpose. Explore three recent client engagements that exemplify our broader purpose: unlocking the potential of those who advance the world.