BCG SPOTLIGHT
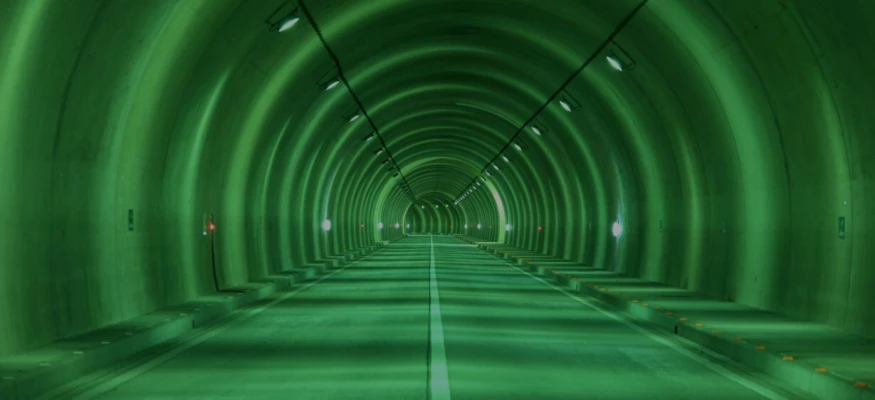
OUR AI ANALYST RECOGNITION
The Forrester Wave™: AI Services, Q2 2024
BCG was named a leader in AI services in The Forrester Wave™: AI Services, Q4 2022, an evaluation of the 9 most significant AI service providers, deeming participating vendors Leaders, Strong Performers, Contenders, or Challengers. Based on its performance, BCG was one of the two companies named a Leader.
LEARN MORE
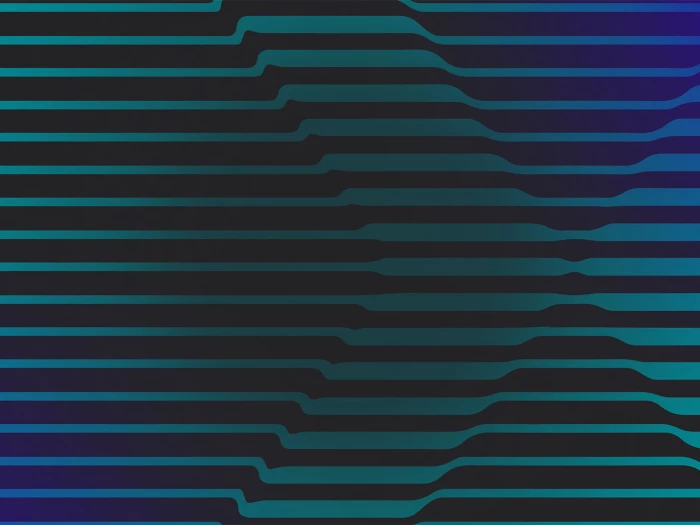

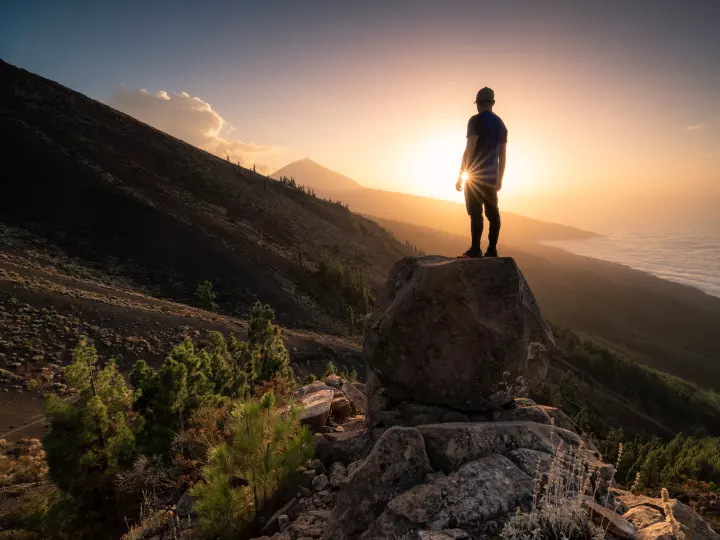

BCG Careers
Go Beyond the Expected
We’re dedicated to helping our clients do amazing things and unlocking the potential of those who advance the world. Join us, and you can too.
APPLY NOW